In the intricate world of metal processing, every stage demands precision, efficiency, and reliability. One integral component often overlooked is the roller—a silent force guiding metal through various processes. These unassuming cylindrical objects play a pivotal role in shaping, forming, and refining metals. Among the myriad of roller materials, one stands out for its exceptional properties—fused silica. Enter Kamroller, a specialized solution by Kamroller Special Ceramics Co., Ltd., designed to revolutionize metal processing.
Section 1: Understanding Fused Silica
1.1 Defining Fused Silica and Its Characteristics
Fused silica, a high-purity form of silicon dioxide, boasts a unique set of characteristics that make it a standout choice for specialized applications. With exceptional thermal stability, low thermal expansion, and high resistance to temperature fluctuations, fused silica is well-suited for extreme high-temperature environments.
1.2 Why Fused Silica for High-Temperature Applications?
The high-temperature resistance of fused silica is a result of its amorphous structure, allowing it to withstand intense heat without compromising its structural integrity. This makes fused silica rollers ideal for applications where traditional materials might succumb to thermal stress.
1.3 Comparison with Other Roller Materials
When pitted against conventional roller materials like steel or ceramics, fused silica emerges as a superior choice. Its low coefficient of thermal expansion reduces the risk of cracking and ensures dimensional stability even under extreme temperature conditions. This characteristic sets fused silica apart in the demanding realm of metal processing.
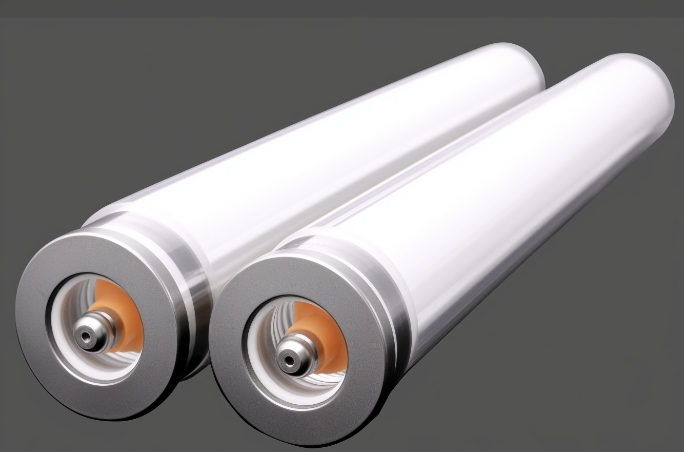
Section 2: The Role of Rollers in Metal Processing
Metal processing is a complex and multifaceted industry, involving various stages from casting and rolling to cutting and finishing. Rollers play a crucial role at each juncture, providing support, guidance, and precision to the metal as it transforms.
2.2 The Importance of Rollers in Metal Processing
Rollers facilitate the movement of metal sheets, ensuring uniform thickness and shape during processes such as rolling and extrusion. They also play a pivotal role in coil processing, where precision is paramount. However, traditional roller materials often face challenges such as wear, thermal stress, and maintenance issues, prompting the need for innovative solutions.
Section 3: Introducing Kamroller
3.1 A Glimpse into Kamroller
Fused Silica Rollers Kamroller, a specialized fused silica roller solution crafted by Kamroller Special Ceramics Co., Ltd., emerges as a game-changer in the metal processing landscape. Engineered with precision and designed for durability, Kamroller aims to address the shortcomings of traditional rollers.
3.2 Unique Features and Properties of Kamroller
Kamroller boasts a high-purity fused silica composition, ensuring superior thermal stability and resistance to thermal shock. Its amorphous structure minimizes the risk of cracks or deformations, even in the most demanding high-temperature applications. The precision engineering behind Kamroller results in a smooth and consistent surface, promoting optimal metal processing.
3.3 Addressing Challenges Faced by Traditional Rollers
Traditional roller materials often struggle with wear and tear, leading to frequent maintenance and downtime. Kamroller, with its enhanced wear resistance, offers a longer lifespan, reducing the need for constant replacements. Its exceptional durability ensures reliability in even the harshest metal processing environments.
Section 4: Benefits of Using Kamroller in Metal Processing
4.1 Improved Heat Resistance and Thermal Stability
Kamroller’s exceptional heat resistance and thermal stability provide a reliable solution for metal processing applications requiring elevated temperatures. This ensures consistent performance and longevity, even in the most demanding industrial settings.
4.2 Enhanced Wear Resistance and Durability
The superior wear resistance of the Kamroller extends its lifespan, reducing the frequency of replacements and associated downtime. This not only translates to cost savings but also enhances the overall efficiency of metal processing operations.
4.3 Reduced Maintenance and Downtime
With Kamroller’s robust design and resistance to wear, maintenance requirements are significantly reduced. This means less downtime for repairs and replacements, allowing for continuous and uninterrupted metal processing operations.
4.4 Increased Product Quality and Precision
The precision-engineered surface of Kamroller contributes to improved product quality and processing precision. Consistency in roller performance translates to uniform metal thickness, shape, and surface finish, meeting the stringent standards of modern metal processing.
Section 5: Applications of Kamroller in Metal Processing
5.1 Rolling Mills and Hot Rolling Processes
Kamroller finds its stride in rolling mills and hot rolling processes, where extreme temperatures and pressure are commonplace. The superior thermal stability of fused silica ensures that Kamroller performs optimally, providing reliable support and guidance to metal sheets as they undergo the intricate process of shaping and flattening.
5.2 Annealing and Heat Treatment Applications
In the realm of annealing and heat treatment, precision is paramount. Kamroller’s exceptional resistance to thermal shock makes it an ideal choice for applications requiring controlled heating and cooling. The uniformity of temperature distribution achieved with the Kamroller contributes to consistent and high-quality outcomes in the annealing and heat treatment processes.
5.3 Surface Treatment and Finishing Processes
When it comes to surface treatment and finishing processes, the quality of rollers directly impacts the final product. Kamroller’s smooth and consistent surface, coupled with its wear-resistant properties, ensures that metal surfaces are treated with precision and finesse. Whether it’s polishing, coating, or other finishing techniques, Kamroller stands out in delivering superior results.
Section 6: Case Studies and Success Stories
6.1 Real-World Examples of Companies Benefiting from Kamroller
Numerous companies across the metal processing industry have experienced tangible benefits with the adoption of Kamroller. From improved efficiency to reduced downtime, these case studies highlight the positive impact of Kamroller on diverse metal processing applications. Companies, both large and small, have reported enhanced productivity and cost savings.
6.2 Testimonials from Users in the Metal Processing Industry
The voice of the end-users in the metal processing industry echoes the success stories associated with Kamroller. Testimonials attest to the durability, reliability, and efficiency of Kamroller in challenging operational environments. Users praise Kamroller for its longevity, reduced maintenance needs, and overall contribution to elevating the standards of metal processing.
Section 7: Tips for Choosing the Right Fused Silica Rollers
7.1 Factors to Consider When Selecting Rollers for Specific Applications
Choosing the right fused silica rollers, such as Kamroller, involves considering various factors. Factors include the temperature range of the metal processing application, load-bearing capacity, and the desired surface finish. Understanding the specific requirements of each application is crucial in making an informed decision for optimal performance.
7.2 Comparison with Other Types of Rollers in the Market
When exploring fused silica rollers, it’s essential to compare them with other types available in the market. Kamroller stands out not only for its high-temperature resistance and wear resistance but also for its longevity and cost-effectiveness. Comparisons with traditional roller materials emphasize the distinct advantages that fused silica, particularly Kamroller, brings to the table in the dynamic landscape of metal processing.
Conclusion
Fused Silica Rollers Kamroller by Kamroller Special Ceramics Co., Ltd. emerges as a revolutionary solution in the realm of metal processing. With its specialized fused silica composition, Kamroller not only addresses the challenges faced by traditional rollers but elevates the standards of efficiency, reliability, and precision in the metal processing industry. As technology advances, innovations like Kamroller pave the way for enhanced capabilities, ensuring a seamless and efficient future for metal processing applications.
Post time: 1 月-16-2024