What applications are there for fused silica rollers?
What can fused silica rollers be used for? There are many different industries where fused silica rollers can be employed. A few typical usages are listed below:
Glass Production:
In the glass business, fused silica rollers are frequently used to make flat glass, glass containers, and optical glass. Throughout the production process, they are utilized to move and hold glass sheets or molten glass.
Industry of Semiconductors:
In the semiconductors industry, fused silica rollers are used for handling, cleaning, and processing wafers. Excellent heat stability, chemical resistance, and minimal particle formation make them perfect for cleanroom settings.
Production of Solar Panels:
As previously noted, fused silica rollers are employed in producing solar panels. Fused silica rollers are essential in the production of solar panels. During the coating, printing, and curing procedures involved in the manufacture of solar cells, they are utilized to move glass substrates and provide stability and accuracy.
Metal Processing:
Hot rolling and continuous casting are two examples of applications for using fused silica rollers. They are appropriate for demanding working situations because they have great thermal shock resistance, high-temperature resistance, and slight thermal extension; fused silica rollers are appropriate for high-temperature heat treatment procedures, including annealing, tempering, and hardening of metals. They provide exceptional thermal stability and shock resistance, allowing precise and controlled heat treatment.
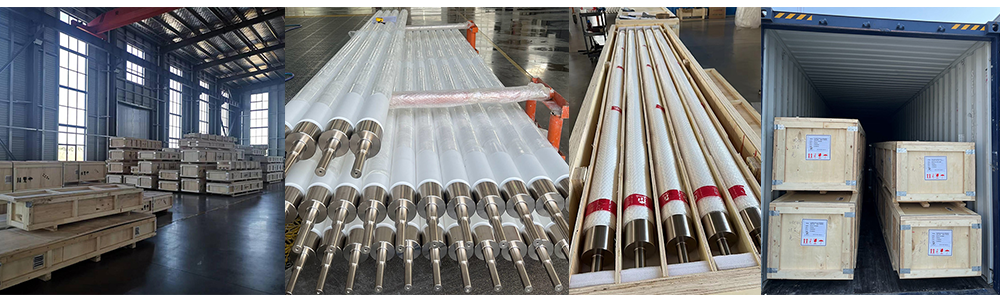
Aerospace:
In the aerospace sector, fused silica rollers are used in procedures including producing composite materials, high-temperature insulation, and thermal barrier coatings. They offer stability, accuracy, and resilience to abrasive conditions and high temperatures.
Natural Energy Resources:
Natural energy resources like oil and gas extraction and processing may use fused silica rollers. In a refinery, liquefaction, or gas processing activities, they might be used in machinery for transporting, directing, or supporting materials.
Petrochemical:
Fused silica rollers can be used in the petrochemical sector to carry, guide, or support materials during operations like refining, making polymers, or producing chemicals. In these applications, its tolerance to acids and high temperatures is advantageous.
How do Fused Silica Rollers work?
Cylindrical parts composed of fused silica are known as fused silica rollers. Fused silica, commonly referred to as fused quartz, is a highly pure kind of silica glass created by melting pure silica and then quickly cooling it to solidify it. Rollers made of fused silica are frequently employed in a variety of industrial applications where precise and controlled movement of materials or components is necessary. What can fused silica rollers be used for? It is use for strong resistance to thermal shock, a low coefficient of thermal expansion, and great thermal stability. These rollers are used in procedures like glass manufacture, semiconductor manufacturing, printing, and other precise sectors. Conveyor systems, annealing furnaces, and other machinery that requires high temperatures and mechanical stability all employ them.
The Exceptionally Versatile Fused Silica Rollers:
Rollers made of fused silica are well recognized for their remarkable adaptability and are frequently employed in a wide range of industrial applications. High-purity, non-crystalline fused silica, commonly referred to as quartz glass, is silicon dioxide. It is a great material option for rollers in many sectors because of its superb thermal, mechanical, and chemical qualities.
- Fused silica possesses outstanding mechanical strength and hardness despite being a glassy material. It is suitable for applications involving material transportation, pressing, or calendaring procedures since it can handle strong weights and pressure. Due to the low friction properties of fused silica rollers, there is less chance of material adhering or causing harm to the treated surface. Their hardness and wear resistance also ensures long service life even in abrasive environments like paper manufacture or textile processing.
- Fused silica exhibits outstanding optical transparency in the ultraviolet, visible, and near-infrared portions of the electromagnetic spectrum. Since rollers are utilized in optical systems, this characteristic makes them useful for industries and solar manufacture.
- Fused silica rollers may be produced with extreme accuracy and close tolerances, guaranteeing reliable and precise performance in various industrial operations. This feature is essential for applications that need exact placement, alignment, or management of materials.
The largest manufacturing facility in Asia for fused silica goods is KAMROLLER:
- The company has been adhering to the concept of “reducing energy loss for the earth”. It provides high-performance ceramic products for the society and reduces the demand for the earth. Kamroller is committed to becoming a global ceramic developer and operator with global influence and competitiveness. Committed to maximizing the value of stakeholders. Kamroller is driven by innovation, pursues excellence, and cherishes the vision of “becoming a leader in the ceramic industry”.
- Kamroller specializes in designing and producing specific ceramic products that can withstand high temperatures and are used in heat treatment situations. Our high-temperature-resistant ceramic rollers and other ceramic goods are used extensively in the semiconductor, automotive, glass, construction, and metal processing sectors. With the help of our strong manufacturing and processing skills, outstanding application engineering specialists, and good customer-focused solutions, we can create strategic collaborations with our clients. From tiny batches to big manufacturing, our ceramic goods and accessories are created to the highest performance standards.
Conclusion:
A special industrial roller constructed from a high-purity silica material is called a fused silica roller. Since it is more temperature and chemical resistant than conventional rollers, it also has better mechanical and electrical qualities. As a result, they have a variety of benefits over them. A high-performance material utilized in several industrial applications is fused silica rollers. We provide outstanding thermal, electrical, and optical qualities. KAMROLLER specializes in designing and producing specific ceramic products that can withstand high temperatures and are used in heat treatment situations. Our high-temperature-resistant ceramic rollers and other ceramic goods are used extensively in the semiconductor, automotive, glass, construction, and metal processing sectors.
Post time: 5 月-15-2023