What are ceramic rollers consist of?
What is ceramic rollers? The explanation is provided below. Ceramic rollers are cylindrical parts used in many industrial applications. They are formed of ceramic materials. These rollers are made to move objects smoothly and effectively, frequently in hot, corrosive conditions. “ceramic” describes a large class of non-metallic, inorganic materials generally derived from silica. Compared to their conventional metal equivalents, ceramic rollers provide several benefits. The rollers can sustain huge loads and resist wear and damage due to ceramics’ great strength and hardness. They also have remarkable thermal stability, enabling them to function at high temperatures without degrading or deforming. Because of this, they are especially beneficial in fields like glass production, steel processing, and high-temperature kilns.
The low friction coefficients of ceramic rollers further minimize energy losses and lessen the requirement for lubrication. In applications like conveyor systems, printing presses, and paper mills, this characteristic helps to increase efficiency and cost-effectiveness. Additionally, ceramic materials are ideal for use in organic processing services and other locations where an introduction to strong chemicals is widespread because they have great corrosion resistance. Ceramic rollers can be produced in various forms, dimensions, and surface treatments to meet individual needs. They are normally well constructed to guarantee accurate dimensions and smooth rotation. Ceramic rollers are manufactured using shaping, sintering, and precision grinding to obtain the appropriate mechanical qualities and surface quality.
Effectiveness of ceramic rollers in ceramic building and their importance:
Rollers made of ceramic are very important and relevant in manufacturing ceramics for buildings. Here are some crucial details emphasizing their importance:
- High-Temperature Resistance:
Ceramics used in construction, including tiles, bricks, and sanitary ware, are fired at high temperatures. Because of its superior thermal stability, ceramic rollers can survive the intense heat of kilns without deforming or deteriorating. Building ceramics are guaranteed to keep their structural integrity and quality during the firing process because of their high-temperature resistance.
- Surface Quality:
Ceramic rollers are essential for preserving the surface quality of construction ceramics. They are made to have even, flat surfaces to reduce the possibility of markings or flaws appearing on the ceramic items when they pass through the kiln. This makes it easier to verify that building ceramics satisfy the requirements for a quality set out by the construction industry and achieves the appropriate visual appeal.
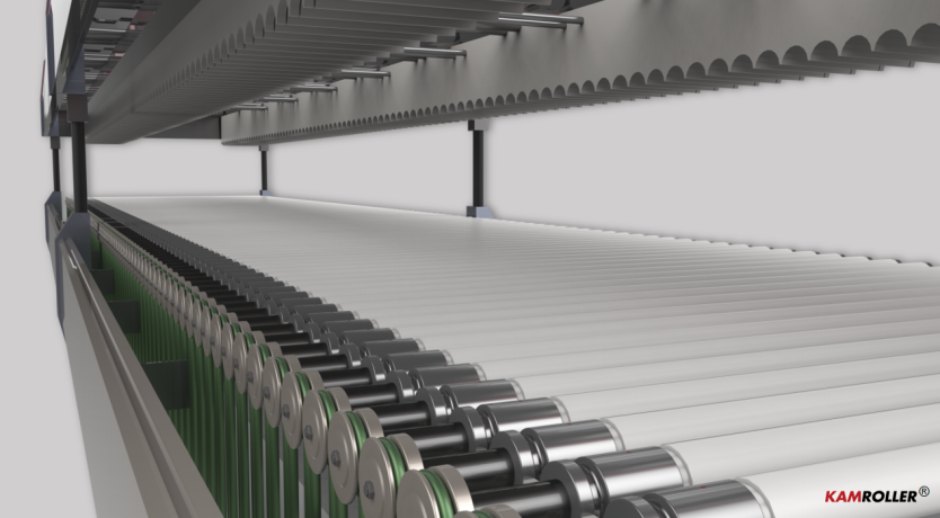
- Support and Alignment:
During various production phases, ceramic rollers offer support and alignment for constructing ceramic items. Whether the ceramics are being shaped, dried, glazed, or fired, they ensure precise location and movement. Proper support and alignment influence the precision and uniformity of the finished goods’ dimensions.
- Chemical Resistance:
Various chemicals glazes, and pigments are employed in manufacturing construction ceramics. Ceramic rollers are ideal for handling and transporting ceramic materials in situations with many chemicals because they provide great resistance to corrosive substances. This resistance aids in shielding the ceramics and rollers from pollution and harm.
- Extended Service Life:
Ceramic rollers offer a longer service life than other roller materials, such as metal or plastic. They are durable in severe industrial environments thanks to their remarkable strength, hardness, and resistance to wear and abrasion. This increased service life translates into cost savings and less downtime in building ceramics.
What features and benefits of ceramic rollers make them more dependable?
Ceramic rollers have great strength and hardness, which enables them to support enormous loads and fend against wear and damage. This quality guarantees its life and durability in industrial applications.
- Because of their outstanding thermal stability, ceramic rollers can withstand high temperatures without deforming or degrading. They can endure the intense heat conditions in businesses like glass production and steel processing.
- The low friction coefficients of ceramic rollers mean less energy is lost during use. The efficiency of systems like conveyor belts, printing presses, and paper mills is increased because of this quality, which results in energy savings and cost-effectiveness. Additionally, it reduces the demand for lubrication, lowering the maintenance needed. Because they can endure the corrosive impacts of acids, bases, and other chemicals, they will work effectively and dependably over the long run.
- Ceramic rollers are used in various sectors, including glass production, steel processing, and the automobile, building ceramic and aerospace industries. Thanks to their adaptability, they are useful in various procedures and situations, which boost output and raise product quality.
Ceramic Rollers’ Function in High-Temperature Applications:
Ceramic rollers are essential in various high-temperature applications, particularly in glass production, steel production, and thermal processing. These rollers are made to function consistently and effectively while withstanding high temperatures and challenging situations. Ceramic rollers are chosen because of their extraordinary ability to withstand high temperatures. They can endure temperatures frequently more than 1000°C (1832°F) without significantly altering their structural integrity. Because of this, they can be used in situations where traditional materials would fail or distort under such high temperatures. Ceramic materials are excellent thermal insulators because they have low heat conductivity. Ceramic rollers aid in reducing heat transmission between various components of the machinery or equipment in high-temperature applications. They promote energy efficiency by serving as thermal insulators, which prevent heat loss and maintain steady temperatures.
Conclusion:
What is ceramic rollers? It can be described in the article above. Ceramic rollers are often employed in a variety of industries and applications. Compared to conventional rollers, ceramic rollers provide several advantages. The biggest manufacturing base of fused silica products in Asia, Kamroller Special Ceramics Co., Ltd. was founded in 2006 by KAMROLLER and China Tianhong Hi-Tech Industrial Ceramics Co., Ltd., using American technology to develop a facility in China’s Crystal Township. The major product applications are in glass, solar energy, aircraft, building ceramics, metal heat treatment, natural energy resources, semiconductors, steel, petrochemical, and other industries. From short runs to scale manufacturing, our ceramic goods and accessories are engineered to perform to the highest standards.
Post time: 5 月-19-2023