What are fused silica rollers?
Fused silica rollers are cylindrical parts constructed of silicon dioxide (SiO2) in their purest form, fused silica. Due to their remarkable qualities and dependability, these rollers are utilized extensively in several industrial applications. As they are exceedingly strong and simple to operate, they are a fantastic way to move big things. They are constructed of a substance known as fused silica, which is a fusion of silicon and oxygen atoms. As a result, they are extraordinarily robust and can support the weight of large items. Are fused silica rollers easy to use? Used silica rollers are incredibly durable, resistant to chemicals, have little friction, and are convenient for various industrial applications. Although they must be handled carefully, they are preferred for operations requiring hot temperatures, corrosive conditions, and fragile materials because of their good material qualities and adaptability.
Are fused silica rollers easy to use?
Due to their exceptional thermal, mechanical, and chemical characteristics, fused silica rollers are extremely adaptable and often utilized in various industries. They may need some particular handling precautions but are typically considered simple. Consider the following significant factors with fused silica rollers:
- Material Characteristics:
Fused silica is a non-crystalline, high-purity silicon dioxide (SiO2) with outstanding qualities. It is very hard, has a low coefficient of thermal expansion, great thermal shock resistance, and is stable at high temperatures. Because of their properties, fused silica rollers are excellent for demanding applications requiring high temperatures and severe environments.
- Ease of Machining:
Fused silica is a brittle material that can be difficult to process. However, highly precise methods and instruments for shaping fused silica rollers have been developed, including diamond-cutting tools and laser machining. Because of their experience working with fused silica, manufacturers can build rollers with precise dimensions and tolerances.
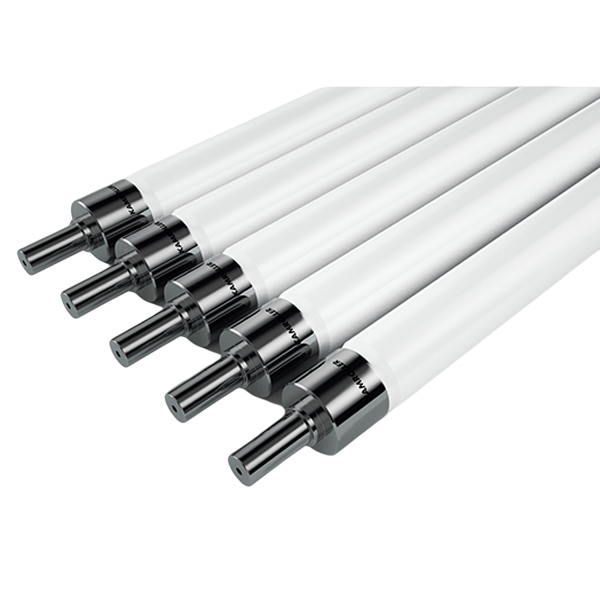
- Versatility:
Fused silica rollers are utilized in various sectors, such as glass manufacturing, semiconductor manufacturing, solar panel manufacturing, and metal processing. They are often used in glass annealing, coating, tempering, and transferring hot metal or glass sheets. The rollers are suited for critical applications due to their smooth surface, high purity, and minimal outgassing characteristics.
Fused silica rollers are resistant to considerable deformation or damage at high temperatures. They can be employed in continuous procedures involving extended heat exposure since they have a high softening temperature (about 1,600°C). In challenging temperature settings, its stability assures continuous performance and lifespan.
- Low Friction and Wear:
The smooth surface of fused silica rollers has low friction characteristics, which lessens the possibility of scratching or destroying sensitive materials. This qualifies them for uses like treating electronic substrates or glass fabrication, where surface quality is important. Because of the rollers’ hardness and wear resistance, they last a long time and require fewer replacements overall.
- Chemical Resistance:
Fused silica rollers are well suited for corrosive applications because of their exceptional resistance to most chemicals, including acids and bases. They guarantee stability and dependability in various industrial processes since they resist chemical reactions and degradation.
- Handling Considerations:
Fused silica rollers are typically simple to handle, but there are a few precautions to consider. They should be handled carefully to avoid accidental breaking due to their fragility. Avoiding collisions or dropping the rollers is crucial, especially when not used. Their integrity may be maintained, and their lifespan may increase with proper handling and storage.
Steps for properly implementing the fused silica roller:
Fused silica rollers must be installed properly to function at their peak and last long. Following these measures will ensure that fused silica rollers are utilized properly:
- Determine Application Requirements:
Understanding the unique needs of your application can help you determine its requirements. Consider the temperature range, chemical exposure, load capacity, required surface finishes, and dimensional constraints. This will make choosing the proper fused silica roller design and attributes easier.
- Choosing the Correct Roller:
To choose the best-fused silica roller for your application:
- Speak with a respected manufacturer or supplier.
- Consider variables like roller diameter, length, surface polish, load capacity, and other customization possibilities based on your unique requirements.
- Make sure the chosen roller complies with the requirements and industry norms.
- Installation Techniques:
According to the manufacturer’s instructions, the proper installation of fused silica rollers. Clean the mounting surfaces to eliminate any dirt or pollutants that can compromise the functioning of the roller. Make that the roller is installed in the system with the necessary mounting hardware or brackets, precisely aligned, and firmly fastened.
- Surface Preparation:
Before installation, prepare the roller surface for the planned application to achieve the best possible bonding and adherence. To remove dust, dirt, or pollutants, carefully clean the surface using a lint-free cloth and an appropriate solvent. Before continuing, make sure the roller surface is dry.
- Roller Mounting:
Determine the best mounting technique for your roller-mounted equipment depending on the demands of your particular application. Fused silica rollers can be installed in several ways, including direct attachment to a machine or conveyor system, shaft mounting, bearing mounting, and bearing mounting. Choose the most appropriate installation technique by consulting the manufacturer’s instructions or consulting a professional.
- Alignment:
The fused silica roller must be precisely aligned to provide smooth operation and prevent early wear or damage. Use precise alignment instruments and procedures to position the roller parallel to the intended direction of motion. This may include changing shafts, bearings, or other parts to ensure appropriate alignment.
- Bearing Lubrication:
If the fused silica roller has bearings, ensure they are oiled adequately before installation. Refer to the manufacturer’s recommendations for information on the required lubricant kind and quantity. Use the recommended lubrication technique to guarantee smooth rotation and prevent bearing damage.
- Load Distribution:
Consider the load distribution throughout the fused silica roller to avoid excessive stress and eventual failure. To retain structural integrity and avoid deformation if the roller bears a significant load, distribute the weight equally over its length and diameter.
- Testing and calibration:
After installation, thoroughly test and calibrate the fused silica roller to ensure it works properly. Look for any indications of excessive heat, vibration, or noise, smooth rotation and good alignment. Conduct pertinent performance testing to ensure the roller satisfies the specified specifications and standards.
- Regular Maintenance:
Implement a routine maintenance regimen to maximize the performance and extend the life of the fused silica roller. This may entail routine lubrication, cleaning, and examination for wear or damage. For advice on maintenance techniques, refer to the manufacturer’s guidelines or seek the advice of a professional.
- Monitoring and troubleshooting:
Keep an eye on the fused silica roller’s functioning while it is in use. Any anomalies, such as increased friction, lower performance, or strange sounds, should be examined. Address any problems immediately to stop more harm and guarantee the roller’s long-term dependability.
Conclusion:
Are fused silica rollers easy to use? Yes, it is. Due to their simple design, great resistance to wear and temperature, and numerous applications in the construction and engineering sectors, fused silica rollers are very important. They are perfect for various applications since they are also stress and corrosion-resistant. Only premium components are used by KAMROLLER to ensure the quality of the finished product. We are dedicated to offering our clients exceptional services and successfully collaborating with domestic and foreign clients. Purchase one at once!
Post time: 5 月-11-2023