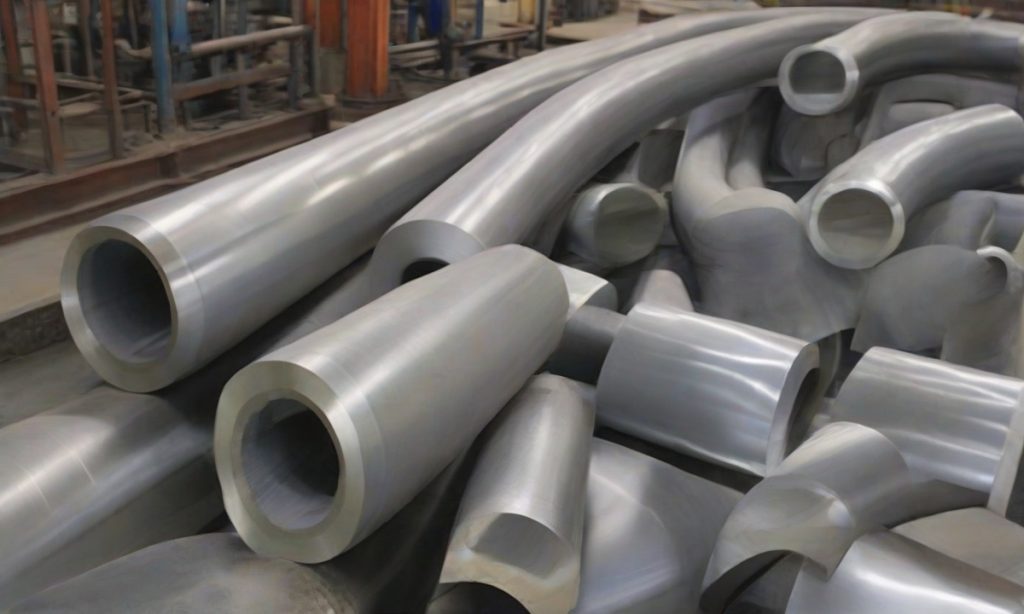
As I delved into the world of industrial machinery, I couldn’t help but be amazed by the remarkable components that make these complex systems work seamlessly. One such component that caught my attention was the fused silica roller. In this comprehensive guide, I will take you on a journey to uncover the incredible attributes of fused silica rollers, focusing on their durability and exceptional heat resistance.
What is a Fused Silica Roller?
A fused silica roller is a specialized cylindrical component used in various industrial applications, known for its exceptional durability and resistance to high temperatures. It is made from a unique material called fused silica, which is a high-purity, non-crystalline form of silicon dioxide (SiO2). Fused silica rollers play a crucial role in facilitating the movement of materials through industrial processes while enduring extreme conditions without deforming or degrading.
Understanding the Basics
Fused silica rollers are a critical part of various industrial processes, including glass manufacturing, steel production, and semiconductor fabrication. These rollers are cylindrical in shape and are made from a special type of material known as fused silica. Fused silica, also referred to as quartz glass, is a high-purity, non-crystalline form of silicon dioxide (SiO2). Its unique properties make it an ideal choice for manufacturing rollers used in extreme environments.
Fused silica rollers are designed to facilitate the movement of materials through various industrial processes with minimal friction and wear. They are used in applications where conventional rollers made from steel or other materials may not withstand the harsh conditions.
Key Characteristics
Now that we have a basic understanding of what fused silica rollers are, let’s explore some of their key characteristics that set them apart from other roller materials.
1. Exceptional Heat Resistance
Fused silica rollers are renowned for their outstanding heat resistance. They can operate in temperatures ranging from hundreds to even thousands of degrees Celsius without deforming or degrading. This remarkable property makes them indispensable in industries that involve high-temperature processes, such as glass tempering and annealing.
2. Superior Durability
Durability is a hallmark of fused silica rollers. They have a long service life, often outlasting conventional rollers made from metals or ceramics. This extended lifespan not only reduces maintenance costs but also improves the overall efficiency of industrial processes.
3. Chemical Inertness
Fused silica is chemically inert, which means it does not react with most substances. This property makes fused silica rollers resistant to corrosion and chemical damage, making them suitable for applications where contact with corrosive materials is inevitable.
4. Low Thermal Expansion
Fused silica has a low coefficient of thermal expansion, which means it expands very little when exposed to temperature changes. This property ensures that the dimensions of fused silica rollers remain stable, even in extreme temperature variations, maintaining the precision required in industrial processes.
Applications of Fused Silica Rollers
Now that we’ve covered the remarkable properties of fused silica rollers, let’s explore some of the specific applications where these rollers play a pivotal role.
1. Glass Manufacturing
Fused silica rollers are extensively used in the glass manufacturing industry. They are employed in processes like glass tempering and annealing, where extreme heat is applied to the glass. The exceptional heat resistance of fused silica rollers ensures that the glass remains smooth and distortion-free during these processes.
2. Steel Production
In the steel industry, fused silica rollers find applications in the production of steel sheets and coils. They are used in hot rolling mills where steel is subjected to high temperatures and pressures. The durability and heat resistance of fused silica rollers contribute to the consistent quality of steel products.
3. Semiconductor Fabrication
The semiconductor industry demands extreme precision and cleanliness. Fused silica rollers are used in semiconductor manufacturing equipment to transport wafers through various processing steps. Their chemical inertness ensures that they do not contaminate the delicate semiconductor materials.
4. Solar Panel Manufacturing
Fused silica rollers are also crucial in the production of solar panels. They are used to convey and process photovoltaic materials at high temperatures, contributing to the efficiency and reliability of solar panels.
5. Textile Industry
In the textile industry, fused silica rollers are employed in dyeing and printing processes. Their durability and chemical inertness make them ideal for handling various chemicals and dyes without degradation.
Advantages of Fused Silica Rollers
Now that we have established the fundamental properties and applications of fused silica rollers, it’s essential to delve deeper into the advantages they offer in various industrial settings. Let’s explore these advantages further:
1. Enhanced Product Quality
Fused silica rollers contribute significantly to the improvement of product quality across different industries. In the glass manufacturing sector, for instance, where precise control of temperatures is critical, these rollers ensure that the final glass products are of superior quality. The rollers’ ability to withstand extreme temperatures without warping or causing inconsistencies in the material is invaluable.
2. Reduced Downtime
One of the most significant advantages of fused silica rollers is their durability. Their resistance to wear and tear means less frequent replacement and maintenance. This leads to reduced downtime in industrial processes, ultimately boosting productivity and minimizing production interruptions.
3. Cost Savings
While the initial investment in fused silica rollers may be higher compared to conventional rollers, their extended lifespan and reduced maintenance costs result in substantial long-term cost savings. Businesses can allocate their resources more efficiently, focusing on other critical aspects of their operations.
4. Environmental Benefits
Fused silica rollers are environmentally friendly due to their composition of natural silica. Moreover, their longevity and reduced need for replacements align with sustainable practices by reducing material waste and energy consumption associated with manufacturing and maintenance.
5. Consistency and Precision
In applications that demand precision and consistency, such as semiconductor manufacturing, the low thermal expansion and dimensional stability of fused silica rollers are paramount. They ensure that the machinery operates with the utmost precision, leading to higher yields and fewer defects in the final products.
Customization Options
Fused silica rollers can be tailored to meet specific industrial needs. Manufacturers offer customization options in terms of size, shape, surface finish, and other parameters. This flexibility allows businesses to select rollers that align perfectly with their unique processes and requirements.
Choosing the Right Fused Silica Roller
Selecting the right fused silica roller for your application is crucial for optimal performance and efficiency. Here are some key factors to consider:
1. Temperature Requirements
Determine the maximum and minimum temperatures your roller will be exposed to. Ensure that the chosen fused silica roller can withstand these temperature ranges without deformation or damage.
2. Size and Dimensions
Consider the size and dimensions of the roller, including its diameter and length. These should match your equipment and application specifications precisely.
3. Surface Finish
The surface finish of the roller can impact material handling and product quality. Discuss the required surface finish with the manufacturer to ensure it aligns with your needs.
4. Load Capacity
Evaluate the load-bearing capacity of the roller to ensure it can support the weight of the materials or products being processed.
5. Chemical Compatibility
If your application involves exposure to chemicals or corrosive substances, confirm that the fused silica roller is chemically compatible with these materials to avoid deterioration over time.
FAQs About Fused Silica Rollers
Q1. Are fused silica rollers more expensive than conventional rollers?
A1. While the initial cost of fused silica rollers may be higher, their exceptional durability and long service life often make them a cost-effective choice in the long run. Their resistance to wear and tear reduces maintenance and replacement costs.
Q2. Can fused silica rollers be customized for specific applications?
A2. Yes, fused silica rollers can be customized to meet the unique requirements of different industries and applications. Customization may include variations in size, shape, and surface finish.
Q3. How do I clean and maintain fused silica rollers?
A3. Fused silica rollers are relatively easy to clean and maintain. They can be cleaned with mild detergents and water. Regular inspection for any signs of wear or damage is recommended, and damaged rollers should be replaced promptly.
Q4. Are fused silica rollers environmentally friendly?
A4. Fused silica is an environmentally friendly material as it is composed of natural silica, which is abundant in nature. Additionally, the long lifespan of fused silica rollers reduces the need for frequent replacements, contributing to sustainability.
Q5. Can fused silica rollers be used in food processing?
A5. Fused silica rollers are not typically used in direct food processing applications. However, they may find use in ancillary equipment such as conveyor systems in food production facilities due to their durability and resistance to cleaning chemicals.
Conclusion
In conclusion, fused silica rollers are a testament to human ingenuity in harnessing the remarkable properties of materials to solve complex industrial challenges. Their exceptional heat resistance, superior durability, chemical inertness, and low thermal expansion make them indispensable in a wide range of applications, from glass manufacturing to semiconductor fabrication.
If you’re looking to supercharge your industrial processes with components that can withstand the harshest conditions, consider the unmatched qualities of fused silica rollers. Their ability to endure extreme heat and maintain precision is a true treasure in the world of industrial machinery.
To explore more about fused silica rollers and their applications, I encourage you to visit KAM Roller’s Fused Silica Ceramic Roller and Quartz Ceramic Guide Groove. These resources provide additional insights into the power and versatility of fused silica rollers in industrial settings.
Unleash the potential of fused silica rollers and revolutionize your industrial processes with their exceptional qualities. Whether you’re in the glass, steel, semiconductor, or any other industry, fused silica rollers are your reliable companions on the journey of efficiency and precision.
Post time: 12 月-19-2023