A brief introduction to fused silica ceramics roller:
- Rollers made of fused silica ceramic are specialist parts that are often employed in many industrial processes, especially those that take place in hot settings. These rollers are carefully constructed from fused silica, a high-purity silicon dioxide, using a melting and solidification process. This produces a material with outstanding resistance to chemical corrosion, good thermal stability, and excellent mechanical strength.
- These rollers are used in various sectors, including semiconductor production, steel processing, and glass making. They assist in the smooth passage of glass sheets through furnaces and kilns during glass manufacturing, retaining dimensional correctness while withstanding extremely high temperatures. These rollers hold the hot metal sheets as they cool in steel mills, guaranteeing equal cooling and reducing warping. Additionally, they support the exact movement of silicon wafers through high-temperature diffusion and annealing processes in the semiconductor manufacturing process, ensuring consistent and dependable electronic component fabrication.
- A fused silica ceramic roller is indispensable in challenging industrial environments because of its exceptional qualities, which include low thermal expansion, good thermal shock resistance, and minimum outgassing. They are a crucial part of industries that depend on strict quality and accuracy requirements because they can withstand extreme temperature cycles, withstand chemical assaults, and provide consistent and reliable support.
Use: Ceramic Fused Silica Roller
- The Fused Silica Roller offers a wide range of applications in several industrial processes where precision material handling and heat stability are crucial. It is essential to the carriage of glass sheets in the glass manufacturing process because it ensures even and smooth movement along the whole production line.
- The Fused Silica Roller controls molten metal transfer during the metal casting process, resulting in a uniform and precise casting. Additionally, it ensures exact placement in continuous manufacturing lines, such as conveyor systems, and offers dependable material movement.
The Benefits of Fused Silica Ceramic Rollers for Industrial Use:
Fused silica ceramic roller has changed the game in the complex world of industrial applications, where harsh conditions such as high temperatures, corrosive environments, and strict quality requirements are common. These outstanding components have ushered in a new era of efficiency, accuracy, and dependability in several industries, including semiconductor fabrication, glass production; steel processing, and glass manufacturing. Let’s explore the benefits that make fused silica ceramic rollers so crucial in various industrial settings.
Remarkable heat Stability:
The fused silica ceramic rollers’ remarkable heat stability is its key feature. High-purity silicon dioxide was carefully heated and solidified to create these rollers with a low thermal expansion coefficient. They can preserve their structural integrity and dimensional precision because of this feature, even when exposed to high-temperature changes. These rollers ensure a smooth flow of operations despite the intense heat of a glass furnace or the quick cooling in a steel mill.
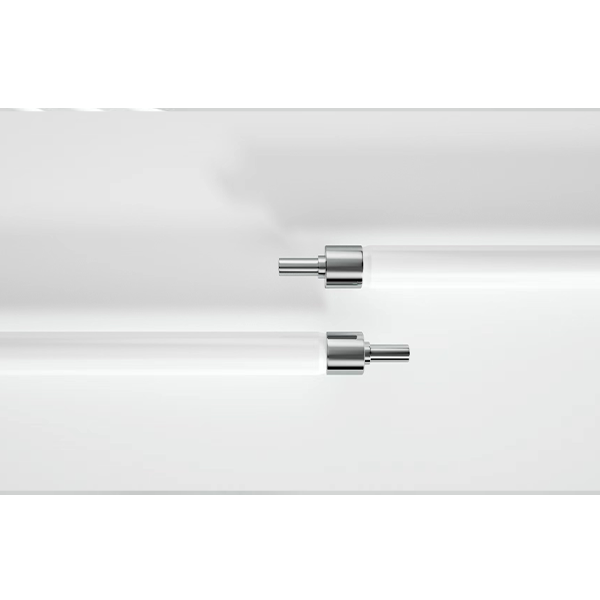
High Thermal Shock Resistance:
This silica ceramic roller is renowned for its capacity to withstand sudden temperature fluctuations without breaking or shattering. These rollers, for instance, make it easier for delicate glass sheets to pass smoothly through hot furnaces when making glass. The integrity of the rollers and the items they support is ensured by the strong thermal shock resistance, which prevents rapid temperature differences from creating thermal stress fractures.
Chemical Corrosion Resistance:
Corrosive substances are frequently present in industrial contexts, which spell disaster for traditional materials. However, rollers made of fused silica ceramic are almost immune to chemical assaults. Due to fused silica’s natural inertness, which contributes to its resilience, the rollers are perfect for many acids, bases, and other corrosive materials. These rollers protect against contamination and provide consistent results in semiconductor production, where precise chemical operations are crucial.
Precision and Consistency:
Many industrial processes depend on accuracy and reliability to succeed. Rollers made of fused silica ceramic perform well in both areas. Because of their consistent, flat surfaces, they offer a solid foundation for sensitive materials like glass sheets and semiconductor wafers. This guarantees that the materials pass through all production phases without bending, distorting, or deviating, ultimately producing higher-quality final products.
Increased Productivity and Yield:
Using fused silica ceramic roller may increase overall efficiency in sectors where productivity is crucial and time is money. Their dependable and regular assistance with materials moving through multiple procedures guarantees a more efficient workflow and fewer flaws in the finished goods. Higher yields and greater profitability are the results of this.
Why is the usage of Fused Ceramic Rollers so crucial?
- Fused ceramic rollers are incredibly versatile and are used in various industries because of their unique properties. Fused quartz is a type of glass made from high-purity silica that has been heated and fused. Roller applications work well because of the resulting product’s excellent thermal and mechanical properties. The importance of Fused Ceramic Rollers in the world of contemporary industrial operations cannot be emphasized. These understated yet essential parts have transformed many industrial and material processing processes, making them essential and indispensable.
- Fused Ceramic Rollers are fundamentally designed with outstanding mechanical strength, wear-resistant characteristics, and heat resistance. These three qualities make them indispensable in fields like the manufacture of glass, metals, textiles, and paper, where high temperatures and continuous operation are commonplace. In contrast to conventional rollers, the fused ceramic type maintains its integrity even under high heat stress, assuring durability and reliable operation.
Conclusion:
Fused silica ceramic roller has replaced the heart in many industrial applications, enabling manufacturing lines’ uninterrupted and smooth operation. Their unmatched mechanical strength, heat resistance, and friction-reducing characteristics highlight their necessity across several industries, advancing modern production toward unmatched efficiency and dependability. With the help of our strong manufacturing and processing skills, outstanding application engineering specialists, and good customer-focused solutions, KAMROLLER can create strategic collaborations with our clients. From tiny batches to big manufacturing, our ceramic goods and accessories are created to the highest performance standards.
Post time: 8 月-17-2023