In the ever-evolving landscape of industrial manufacturing, companies are constantly seeking innovative solutions to optimize their processes and enhance productivity. One such solution that has gained significant traction is the utilization of high-quality materials and components.
Among these, fused silica roller manufacturers & suppliers have emerged as crucial partners in various industries, revolutionizing the way manufacturing processes operate.
In this blog post, we will delve into the world of fused silica roller manufacturers & suppliers, exploring their significance in industrial growth and offering insights into their benefits and applications.
Understanding Fused Silica Rollers:
Fused silica rollers are precision-engineered components used in diverse industrial applications. These rollers are manufactured using fused silica, a high-purity, amorphous form of silica that exhibits exceptional thermal, mechanical, and electrical properties.
Fused silica is created by melting pure silica at high temperatures and then rapidly cooling it, resulting in a glass-like material with outstanding characteristics.
The Role Of Fused Silica Rollers In Industrial Processes:
Fused silica rollers play an important role in a variety of industrial processes. They are used in the manufacturing of semiconductors, optical fibers, and other electronic components; in applications that require high-performance mechanical strength, such as in aircraft engines; and for applications that require high thermal stability and low thermal expansion coefficient.
1) Heat Treatment Applications:
Fused silica rollers find extensive use in heat treatment processes such as annealing, tempering, and quenching. Their high thermal stability and low thermal expansion coefficient make them ideal for applications requiring uniform heat distribution and controlled cooling rates.
These rollers ensure precise temperature control and enhance the efficiency of heat treatment operations, resulting in improved product quality and reduced cycle times.
2) Glass Manufacturing Industry:
The glass manufacturing industry heavily relies on fused silica roller manufacturers & suppliers for their exceptional properties. These rollers are utilized in glass-forming processes, including glass melting, glass annealing, and tempering.
Fused silica rollers provide superior resistance to thermal shock, chemical corrosion, and deformation at elevated temperatures. Their smooth surface and low friction characteristics contribute to the production of high-quality glass products with minimal defects.
3) Semiconductor and Electronics Industry:
Fused silica rollers play a vital role in the semiconductor and electronics industry. With the increasing demand for advanced electronic devices, the production processes require precise handling of delicate materials.
Fused silica roller manufacturers & suppliers offer rollers that are used in various stages of wafer processing, including lithography, chemical vapor deposition (CVD), and etching. These rollers ensure accurate alignment, reduce contamination risks, and offer excellent resistance to chemical agents, thereby enhancing manufacturing efficiency.
4) Steel and Metal Processing:
In the steel and metal processing industry, fused silica roller manufacturers & suppliers are sought after for their expertise. These rollers are employed in applications such as continuous casting, hot rolling, and cold rolling.
The exceptional thermal shock resistance and high mechanical strength of fused silica rollers enable them to withstand extreme conditions encountered during metal forming processes. Fused silica rollers provide uniform pressure distribution, resulting in improved surface quality and dimensional accuracy of metal products.
Choosing Reliable Fused Silica Roller Manufacturers & Suppliers:
When it comes to sourcing fused silica rollers, it is crucial to partner with reputable manufacturers & suppliers. Here are some key factors to consider:
Quality Assurance and Certification:
Opt for fused silica rollers manufacturers & suppliers that prioritize quality control and adhere to international standards. Certifications such as ISO 9001:2015 demonstrate their commitment to delivering reliable and consistent products.
Technical Expertise and Customization Options:
Look for fused silica rollers manufacturers & suppliers with a strong technical background and expertise in producing. They should be capable of providing tailored solutions to meet specific industrial requirements and offer guidance on material selection and design optimization.
For example, Kamroller, from the hometown of Crystal in China, combines the advanced technology of the United States with their own experience. They have accumulated a lot of experience in the industry, and constantly improve production technology and product quality through customer feedback.
Production Capacity and Timely Delivery:
Consider fused silica rollers manufacturers & suppliers with sufficient production capacity to meet your demand. Timely delivery is crucial to ensure uninterrupted manufacturing processes, so choose suppliers with a proven track record of delivering products on time.
After-Sales Support and Services:
Evaluate the level of after-sales support offered by fused silica rollers manufacturers & suppliers. This includes technical assistance, troubleshooting, and efficient customer service. Reliable manufacturers & suppliers stand by their products and provide comprehensive support throughout the product lifespan.
Benefits Of Utilizing Fused Silica Rollers:
Kamroller’s fused silica rollers are more durable than other materials such as aluminum oxide, which makes them ideal for a wide range of applications including:
Enhanced Product Quality:
The exceptional thermal stability and low coefficient of thermal expansion of fused silica rollers contribute to consistent heat distribution and controlled cooling rates. This leads to improved product quality, reduced defects, and enhanced dimensional accuracy.
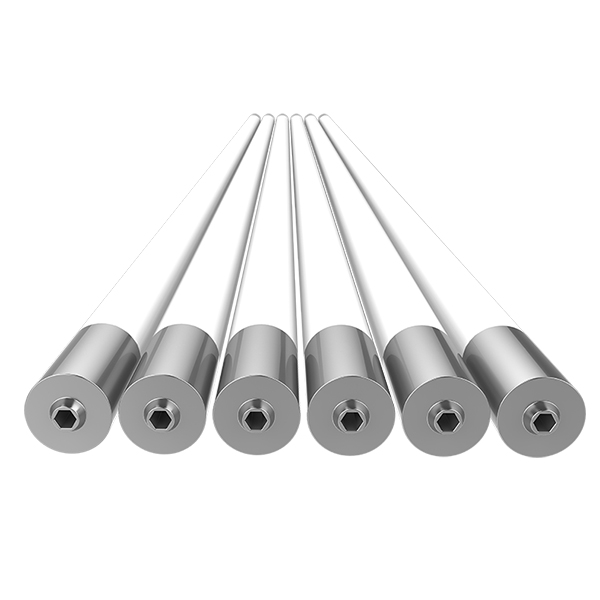
Increased Operational Efficiency:
Fused silica rollers offer low friction and excellent wear resistance, resulting in reduced energy consumption and maintenance costs. Their smooth surface enables smooth material flow, minimizing the risk of surface imperfections and downtime.
Extended Lifespan and Cost Savings:
Compared to conventional rollers, fused silica rollers exhibit superior durability and resistance to thermal and mechanical stresses. Their extended lifespan reduces the need for frequent replacements, resulting in significant cost savings in the long run.
Final words:
The utilization of fused silica roller manufacturers & suppliers has become indispensable in various industrial sectors, revolutionizing manufacturing processes and contributing to overall industrial growth.
Their exceptional properties, including high thermal stability, low thermal expansion coefficient, and superior resistance to thermal shock and chemical corrosion, make them the ideal choice for heat treatment, glass manufacturing, semiconductor, and electronics, as well as steel and metal processing applications.
To ensure the seamless integration of fused silica rollers into manufacturing operations, it is vital to collaborate with reliable manufacturers & suppliers, such as Kamroller, who prioritize quality, technical expertise, and timely delivery.
Post time: 6 月-08-2023