What is meant by fused silica rollers?
- Fused silica rollers are cylinder-shaped parts composed of fused silica glass material. Fused silica is a pure, non-crystalline kind of silicon dioxide (SiO2) produced by melting quartz or silica sand, then cooling it.
- Rollers made of fused silica are well-recognized for having great heat and chemical resistance, which makes them appropriate for many industrial uses. They have a low coefficient of thermal expansion; therefore, temperature changes do not cause them to expand or contract dramatically. They are extremely stable and thermally stress-resistant thanks to this characteristic.
- These rollers are frequently employed in high-temperature settings, such as the manufacture of glass, where they support and direct sheets of glass or molten glass throughout production procedures. Fused silica rollers ensure accurate and streamlined movement of glass materials by providing great dimensional stability, minimal friction, and high wear resistance.
- In addition, these silica rollers are employed in procedures like wafer handling and lithography in other sectors, such as semiconductor production. Additionally, they may be used to produce optical fiber, which needs exact control and guidance.
- Silica rollers are prized for their remarkable thermal qualities, chemical resistance, and dimensional stability, making them crucial in several industrial processes.
The Incredible Strength and Versatility of Fused Silica Rollers:
Because of its extraordinary strength and adaptability, fused silica rollers are highly prized in various industrial applications. These rollers are constructed of fused silica, a form of glass manufactured by melting and cooling quartz or silica sand. Let’s look at the qualities that provide fused silica rollers their strength and adaptability.
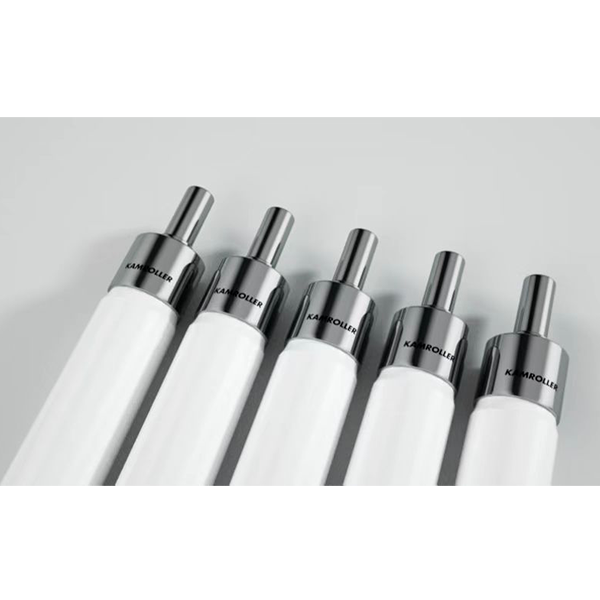
- Exceptional thermal resistance:
The remarkable temperature resistance of silica rollers is one of its main advantages. High temperatures won’t cause them to change or lose their mechanical qualities. Due to its extremely low coefficient of thermal expansion, fused silica does not considerably expand or contract when subjected to temperature changes. This quality makes the rollers excellent for use in high-temperature situations, enabling them to keep their dimensional stability even in great heat.
These silica rollers provide good chemical resistance in addition to heat resistance. They are inert and resistant to deterioration or reaction when exposed to various chemicals and acidic substances. This qualifies them for use in fields like chemical processing, where contact with potent chemicals is prevalent.
- Dimensional stability:
Another important benefit of fused silica rollers is their dimensional stability. They exhibit exceptional resilience to deformation under load and very little shrinkage. As a result, the rollers keep their form and structural integrity even when put under intense pressure or stress, providing smooth and accurate movement throughout industrial operations.
- Wear resistance:
Rollers made of fused silica also have great wear resistance. Without substantial wear or deterioration, they can survive repeated touch and friction. They are the perfect choice for situations where toughness and long service life are essential. For instance, these silica rollers manufacture molten glass or glass sheets and can withstand continuous contact and friction without wearing out.
- Versatility:
The usage of these silica rollers in a variety of sectors demonstrates their adaptability. They are often used in the annealing, tempering, and glass-forming steps of the manufacture of glass. The rollers provide high-quality manufacturing by giving the glass accurate direction and robust support.
What are the applications of fused silica rollers?
Rollers made of fused silica are special and have several benefits over other types of rollers. They are ideal for industrial applications since they are incredibly tough and long-lasting. They are perfect for applications that need heat resistance since they are also lightweight and have great thermal characteristics. These silica rollers are utilized in crucial procedures, including wafer handling and lithography in the semiconductor industry. They are suited for maintaining the sensitive semiconductor wafers’ integrity and purity during manufacture because of their outstanding dimensional stability and minimal particle formation.
- Optical fiber:
Additionally, optical fiber is produced using fused silica rollers. They are used to direct and regulate the fiber drawing procedure, assuring consistency and the creation of high-quality fiber. The exceptional wear resistance and minimal friction of fused silica rollers make them ideal for this demanding application. They are also employed in several other industrial processes that call for accurate motion, stability, and resistance to harsh chemicals and high temperatures. These involve producing ceramics, processing metals, and other things.
- Glass Manufacturing:
These silica rollers are essential to the production of glass. During production, they support and move glass sheets or molten glass. High-quality glass products are produced due to the rollers’ temperature resilience, dimensional stability, and minimal friction, guaranteeing smooth movement and exact control of the glass.
- Semiconductor industry:
Rollers made of fused silica are often utilized in the semiconductor sector. They are used in crucial procedures like wafer handling, which gives delicate semiconductor wafers robust, dependable support. The rollers are perfect for preserving the purity and integrity of the wafers during manufacture due to their dimensional stability, minimal particle formation, resilience to high temperatures, and chemical resistance.
- Ceramics Manufacturing:
These silica rollers are also utilized in the production of ceramics. They aid and direct ceramic sheets or components throughout the heating or sintering operations. Due to the rollers’ great thermal stability and resistance, they can endure the high temperatures encountered during the manufacturing of ceramics, enabling accurate temperature control and even heating or cooling of the ceramic materials.
- Heat Treatment:
These silica rollers are utilized in operations like annealing and tempering that need heat treatment. The rollers can transport and handle materials at high temperatures without deforming or degrading due to their outstanding heat resistance and dimensional stability. They guarantee even heating and cooling, contributing to ideal material qualities.
Conclusion:
Fused silica rollers are a crucial piece of machinery used in several industries. They have a variety of advantages, including high temperature and corrosion resistance, low weight, and exceptional durability. They are an excellent option for various applications due to their considerable versatility. The biggest manufacturing base of fused silica products in Asia, Kamroller, was founded in 2006 by KAMROLLER and China Tianhong Hi-Tech Industrial Ceramics Co., Ltd., who leveraged American technology to develop a facility in China’s “Crystal Township.” Customers worldwide receive high-quality goods and services from our businesses and organizations.
Post time: 7 月-14-2023