What is meant by ceramic rollers?
Due to their excellent qualities and advantages over conventional roller materials, ceramic rollers are cylindrical components constructed of ceramic materials utilized extensively in many industries. Applications that need high-temperature resistance, chemical inertness, dimensional stability, and wear resistance are the ones that most frequently employ these rollers.
Explore the features and advantages of ceramic rollers:
Advanced ceramic materials like alumina (aluminium oxide), silicon nitride, or silicon carbide are the main building blocks of ceramic rollers. These materials are ideal for demanding industrial applications because of their superior thermal and chemical characteristics. They can sustain very high temperatures without deforming or losing their mechanical qualities. They are often employed in procedures involving high temperatures, such as the production of glass, the heat treatment of metals, and the creation of semiconductors.
Chemical Inertness:
Ceramic materials can endure exposure to acids, alkalis, solvents, and other strong chemicals and are very resistant to chemical corrosion. This qualifies ceramic rollers for use in petrochemical and other sectors with tough chemical conditions.
Dimensional Stability:
Ceramic rollers have limited thermal expansion, so they keep their form and dimensions even after sudden temperature fluctuations. This quality guarantees accurate and reliable performance in various industrial operations, including manufacturing steel and ceramics for building.
Wear Resistance:
Ceramic rollers have a great deal of wear resistance, which enables them to tolerate abrasive pressures and keep working effectively for a long time. Applications involving continuous or repetitive contact with other materials, such as those in the steel and glass industries, benefit greatly from this feature.
Low Friction:
Ceramic rollers have a low coefficient of friction, reducing the possibility of surface abrasion and enabling fluid movement and rotation. Applications requiring accurate positioning and less surface wear, such as handling and polishing semiconductor wafers, benefit from this characteristic.
Surface Finish:
Smooth surfaces are commonly used for manufacturing ceramic rollers, guaranteeing low friction and simple material release. Ceramic rollers can be used in applications in the semiconductor, glass, and ceramic industries because of their smooth surface, which also aids in preventing product contamination or marking on delicate items.
Longer Service Life:
Because of their superior qualities, ceramic rollers often have a longer service life than other roller materials. For sectors that depend on these rollers, this leads to decreased maintenance and replacement costs, offering long-term cost benefits.
How do you use a ceramic roller?
How do you use a ceramic roller? The method of using a ceramic roller is simple. To ensure a uniform distribution of the substance on the roller surface, first load the roller by rolling it back and forth in the material you wish to apply, such as paint or ink. Apply the material, beginning at one end of the surface, rolling the ceramic roller in a single direction. Keep your pressure constant and slightly overlap your strokes to ensure uniform coverage. Between applications, wash the roller, and store it properly for further use. Remember to adhere to the manufacturer’s special directions for the best results.
Different applications of ceramic roller:
Ceramic rollers are used in various applications in various sectors, highlighting their excellent qualities such as high-temperature resistance, chemical inertness, dimensional stability, and wear resistance. For various manufacturing operations where accurate handling, heat control, and durability are crucial, ceramic rollers are a favoured option because of these characteristics. It’s important to remember that precise standards might change based on the sector and application. Ceramic roller compositions, size, and surface treatments may therefore be altered to match the particular requirements of each industry. Due to its outstanding qualities and adaptability, ceramic rollers are utilized extensively across various sectors. Let’s examine how do you use a ceramic roller? And precise uses of ceramic rollers in several industries:
Glass Industry:
According to the industry, ceramic rollers are essential to the production of glass. They are used to fabricate float glass, annealing, and glass tempering. Ceramic rollers guarantee exact and consistent glass thickness during manufacturing by providing high-temperature resistance, great thermal shock resistance, and a smooth surface.
Solar Energy:
Ceramic rollers are used in the fabrication of photovoltaic modules and solar panels. They are utilized for accurate alignment and support during manufacturing and coating operations. Because of their great wear resistance, chemical inertness, and high-temperature durability, ceramic rollers are the best choice for handling sensitive solar cell components.
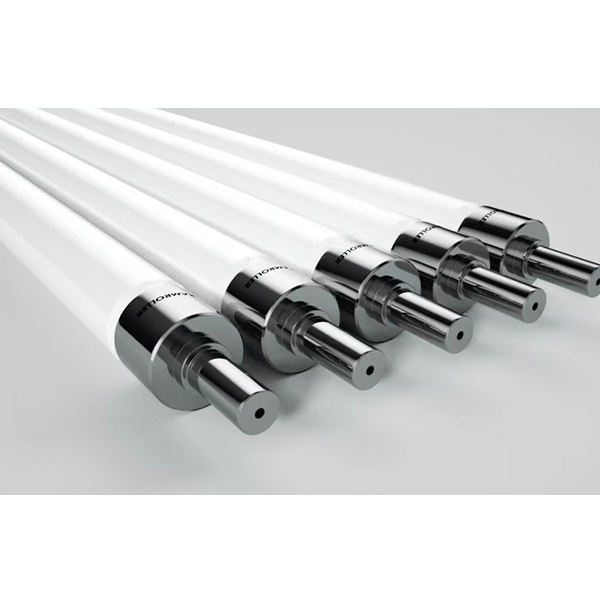
Construction Ceramics:
Ceramic rollers make ceramic tiles, bricks, and sanitary ware in construction. They are used for burning and sintering procedures in furnaces and kilns. Ceramic rollers ensure consistent and superior ceramic products by offering great resistance to chemical assault, dimensional stability, and severe temperature conditions.
Metal Heat Treatment:
Annealing, quenching, and tempering are just a few of the metal heat treatment procedures that frequently include ceramic rollers. They are used in roller hearth furnaces and continuous furnaces. Ceramic rollers have the minimal thermal expansion, can sustain high temperatures, and distribute heat evenly, all of which assist in avoiding deformation and retaining the dimensional correctness of the metal components being treated.
Natural Energy Resources:
Oil, gas, and mineral extraction and processing are two areas where ceramic rollers are used to produce natural energy. They are used in furnaces, rotary dryers, and kilns for high-temperature applications. Ceramic rollers ensure dependable and effective operations in extracting and processing natural resources by withstanding abrasive chemical conditions, erosion, and thermal cycling.
Semiconductor Industry:
Ceramic rollers are essential to producing semiconductors, according to the semiconductor industry. In wafer handling, polishing, and coating activities, they are employed. Ceramic rollers are ideal for semiconductor manufacture’s precise and sensitive needs because they offer good dimensional stability, minimum particle formation, resistance to solvents, and abrasion.
Steel industry:
Continuous casting, hot rolling, and annealing are just a few of the steel production processes that use ceramic rollers. Throughout these operations, they are employed to support and guide steel products. Ceramic rollers ensure smooth and effective steel manufacturing by providing high-temperature resistance, superior wear resistance, and low friction.
Petrochemical Industry:
Ceramic rollers manufacture chemicals, polymers, and plastics in the petrochemical industry. They are used in drying systems, kilns, and reactors. Ceramic rollers provide dependable and continuous operation in abrasive petrochemical conditions by offering resistance to high temperatures, chemical corrosion, and wear.
Conclusion:
The ceramic roller can swiftly and smoothly transport materials because of its low coefficient of friction. Customers throughout the world may purchase high-quality goods and services from KAMROLLER organizations. We are renowned for producing high-quality goods and providing clients value-added services that may help them choose the ideal diffuser type for their building. In addition to being long-lasting, our goods are also resistant to high temperatures, chemicals, dimensional instability, and wear.
Post time: 5 月-09-2023