What are rollers for tempering glass?
What are glass tempering rollers? Specialized equipment used in the glass tempering process includes glass tempering rollers. Glass is subjected to a heat treatment technique known as tempering to enhance its strength and make it safer. The glass is heated to a high temperature and then quickly cooled. Internal tensions are produced in the glass, as a result, increasing its strength and impact resistance. To complement the functionality of glass tempering, tools like the US address generator can be valuable for businesses in managing logistics and streamlining their operations, especially when shipping glass products safely. Typically, they are cylindrical rollers composed of steel or another heat-resistant material. These rollers are employed in glass tempering furnaces where the glass is heated and cooled.
The process and design of the glass tempering rollers:
The glass is fed into the furnace while tempered and put on the rollers. The rollers support and move the glass through the furnace’s heating and cooling zones. The temperature of the glass rises as it passes through the furnace, becoming very close to its softening point. While the glass is heated, the rollers keep it straight and in form. Quenching quickly cools the glass when it reaches the correct temperature.
Jets of air or other cooling medium are directed onto the glass surface during the quenching process—the aid of the glass tempering roller in regulating the cooling process and preserving the glass’ alignment. For the glass to be heated and cooled evenly and to keep its flatness and surface quality, the glass tempering rollers’ design is essential. They must resist warping or distortion at high temperatures and abrupt temperature fluctuations. The rollers are frequently coated with a heat-resistant substance to increase their endurance and reduce the possibility of scratching or harming the glass surface.
Considering the Characteristics of Glass Tempering Rollers:
Glass tempering includes a heating glass to a high temperature and then quickly cooling it to strengthen its strength. Glass tempering rollers are essential. These rollers support and move the glass when heated and cooled in the tempering furnaces. The materials utilized, the roller design, and the performance characteristics must all be understood to investigate the qualities of glass tempering rollers. Consider the following important factors:
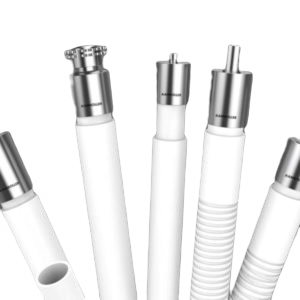
Material:
To endure the harsh circumstances of the tempering process, glass tempering rollers are often built from specialized high-temperature materials. Ceramic, graphite or a mixture of both is frequent material. Excellent thermal stability and thermal shock resistance may be found in these materials.
Thermal Conductivity:
The roller material’s thermal conductivity is crucial since it impacts heat transfer during tempering. A temperature gradient across the glass is necessary for the proper strength and stress distribution, and low thermal conductivity helps maintain this gradient. For instance, graphite rollers provide effective thermal insulation and enable regulated cooling.
Surface Finish:
Carefully monitoring the roller’s surface finish will help to avoid chipping or breaking the glass during shipping. It is preferable to have smooth surfaces with few flaws to provide appropriate contact and prevent any potential flaws on the glass surface.
Roller Design:
The glass tempering roller’s design is essential for ensuring efficient and dependable glass transportation. To increase grip and reduce glass sliding, the rollers, which are normally cylindrical, may feature ridges, grooves, or other surface patterns. The roller’s length and diameter have been adjusted to handle a range of glass thicknesses and sizes.
Durability and Wear Resistance:
Glass tempering rollers must withstand extended periods of exposure to high temperatures and frequent thermal cycling without suffering considerable wear or distortion. High strength, great dimensional stability, and resistance to chemical interactions with glass or other components involved in the process should all be characteristics of the material utilized.
Load Capacity:
Glass tempering rollers must have a load capacity that allows them to sustain the weight of the glass being treated. The rollers’ strength, diameter, and design all affect how much weight they can support. Sufficient load-bearing capability is required to avoid roller deformation and ensure appropriate contact with the glass surface.
Maintenance and Cleaning:
During the tempering process, impurities like glass fragments or coatings may collect on the rollers used for tempering glass. Consequently, simplicity of upkeep and cleaning is a crucial factor. Some roller designs include elements like easily replaceable sleeves or detachable sleeves.
What glass tempering rollers do you choose?
In the glass tempering process, glass tempering rollers offer a number of advantages. Glass is strengthened with tempering rollers, which subject the material to fast cooling after severe heating.
Applying a compressive force to the glass’ surface during this procedure greatly increases its strength and breaking resistance. Tempered glass is generally stronger than annealed glass for a glass of the same thickness. Due to its distinctive fracture pattern, tempered glass is regarded as safety glass. Compared to ordinary glass, which produces sharp, jagged shards when it breaks, tempered glass shatters into small, granular bits with rounded edges, lowering the risk of catastrophic injury. To achieve this safety attribute, tempering rollers are essential. When compared to standard glass, tempered glass is more resistant to thermal stress brought on by temperature variations. Rapid temperature variations may be absorbed without it breaking or shattering. In locations with high-temperature changes, this characteristic is extremely advantageous.
Conclusion:
What are tempering glass roller? In the article above, it is explained. Rollers used in the glass tempering process are crucial piece of equipment. It contributes to the glass’s greater toughness and offers the end user safety advantages, including improved shatter resistance. Any industry may benefit from understanding its consumers’ demands and forming strategic connections with them. Your excellent manufacturing and processing skills and knowledge of application engineering allow you to provide your clients with specialized, cost-effective solutions adapted to their individual needs. KAMROLLER Mutual advantages from this partnership include improved product development, increased effectiveness, and higher customer satisfaction.
Post time: 5 月-10-2023